Reportage sur la qualité Audi : Haute résolution
Si Audi est devenu LA référence à suivre dans le monde du « premium », c’est parce que le constructeur met tout en œuvre, depuis des décennies, pour tendre vers la perfection. Nous sommes allés à Ingolstadt, rencontrer dans les labos secrets les « responsables qualité » du constructeur, pour comprendre comment ils travaillent. Voici un éclairage inédit et passionnant sur ces hommes de l’ombre où le mot « hasard » n’a pas sa place…
Pour plagier un ancien slogan d’une marque automobile, je dirais « vous n’imaginez pas tout ce qu’Audi peut faire pour vous ». Nous en avions une petite idée, mais à mille lieux de la réalité. En arrivant aux portes de l’usine historique d’Audi, nous devons montrer patte blanche et laisser tout appareil susceptible de prendre des photos. Nous pénétrons dans un véritable sanctuaire, un « saint des saints » mieux protégé que fort-Knox. Werner Zimmermann, directeur de la qualité Audi, est à la tête d’une équipe de 300 personnes, exclusivement dédiée à ce qui fait qu’une Audi est une Audi. Il nous reçoit et tente de nous faire comprendre ce qu’est sa notion de la « qualité ».Pour plagier un ancien slogan d’une marque automobile, je dirais « vous n’imaginez pas tout ce qu’Audi peut faire pour vous ». Nous en avions une petite idée, mais à mille lieux de la réalité. En arrivant aux portes de l’usine historique d’Audi, nous devons montrer patte blanche et laisser tout appareil susceptible de prendre des photos. Nous pénétrons dans un véritable sanctuaire, un « saint des saints » mieux protégé que fort-Knox. Werner Zimmermann, directeur de la qualité Audi, est à la tête d’une équipe de 300 personnes, exclusivement dédiée à ce qui fait qu’une Audi est une Audi. Il nous reçoit et tente de nous faire comprendre ce qu’est sa notion de la « qualité ».
Voilà un terme assez subjectif qui veut à la fois tout dire, et ne rien dire. Une précision de sa part s’impose. « Par qualité, certains n’entendent que la solidité, la fiabilité. Pour nous, c’est aussi du prestige, du raffinement, mais également l’accès aux toutes dernières technologies. La dernière A8 en est le plus bel exemple, puisqu’elle embarque plus de 100 boîtiers interconnectés et qu’elle propose plus de 500 fonctions. Nous entrons dans l’ère du digital, ce qui va nous amener à connaître, rapidement, de profonds bouleversements, même si la qualité reste, et restera, la compétence clé d’Audi ».
L’ère digitale
Evidemment, par « digital », nous pensons tout de suite au cockpit virtuel et aux voitures connectées. Mais ceci n’est qu’un petit aspect du champ des possibles… En fait, Audi travaille surtout sur des échelles dignes de l’infiniment petit, que nous ne pouvions imaginer. Tout cela commence dans des laboratoires secrets de Recherche et Développement, où nous avons eu exceptionnellement accès. Il y est essentiellement question de « semi-conducteurs », des éléments composés de silice désormais indissociables d’une voiture moderne, puisque 80% des innovations reposent sur eux. Pour vous donner idée, il y en a près de 8000 dans une Audi haut de gamme d’aujourd’hui, mais aussi près d’une centaine de boitiers électroniques composés de platines, de puces, de processeurs. D’où la nécessité de disposer dans ces labos de scanners par électrons, mais aussi de microscopes électroniques haute performance pouvant aller au centre de la matière… afin de mieux l’observer et la comprendre !
Ainsi, la suppression de la classique mollette MMI dans la nouvelle A8 a demandé une radiographie ultra-détaillée de cette pièce par balayages, pour ensuite creuser la matière et l’analyser. Une prouesse rendue possible par un faisceau d’ions et d’électrons, pour observer avec précision les différentes surfaces. Le tout en très haute résolution, avec la possibilité d’agrandir 100 000 fois l’image d’un composant Pourquoi ? Pour mieux comprendre la matière, voir ses traces d’usinage, ses défauts, ses déformations. Ici, on n’est plus à l’échelle du micron mais plutôt à celle de la nano particule. En clair, sur le moniteur de contrôle, une puce électronique ressemble de loin à la vue aérienne d’une ville, sur laquelle il est possible de zoomer presque à l’infini, jusqu’aux pores de la matière ! Cette étude, au cœur de chaque élément, donne à Audi une longueur d’avance sur la concurrence, avec des connaissances et une compréhension unique des matériaux.
Werner Zimmermann poursuit, et ce qui suit donne le vertige… « Le fil d’un composant, un contacteur ou la coupe d’un écran tactile n’ont plus de secrets pour nous. On procède à de nombreux tests sur les matériaux, pour trouver d’éventuelles faiblesses afin de supprimer ces points critiques. Cela se fait par des analyses chimiques, mais aussi plus simplement en les soumettant à des températures extrêmes en laboratoire. Ici, nous avons une technologie high-tech, au service de dispositifs high-tech. Nous sommes en automobile un pionnier en travaillant de la sorte, et cela fait déjà plus de 4 ans que nous procédons ainsi ! ».
Né sous « X »
Mais ceci n’est qu’un aspect du métier. Chez Audi, l’ingénierie est également étendue à la légèreté et la résistance des matériaux de pièces invisibles qui semblent anodines, comme un réservoir de carburant. Audi explore depuis quelques années déjà la voie prometteuse de l’hydrogène, et cela implique de nombreuses contraintes. Déjà, le volume nécessaire est plus important que pour l’essence, ce qui réclame de fabriquer sur-mesure un réservoir de forme torturée, qui va combler le moindre espace libre sous le châssis, afin de ne pas empiéter dans le coffre ou l’habitacle. Enfin, la sécurité reste ici bien sûr au cœur des préoccupations.
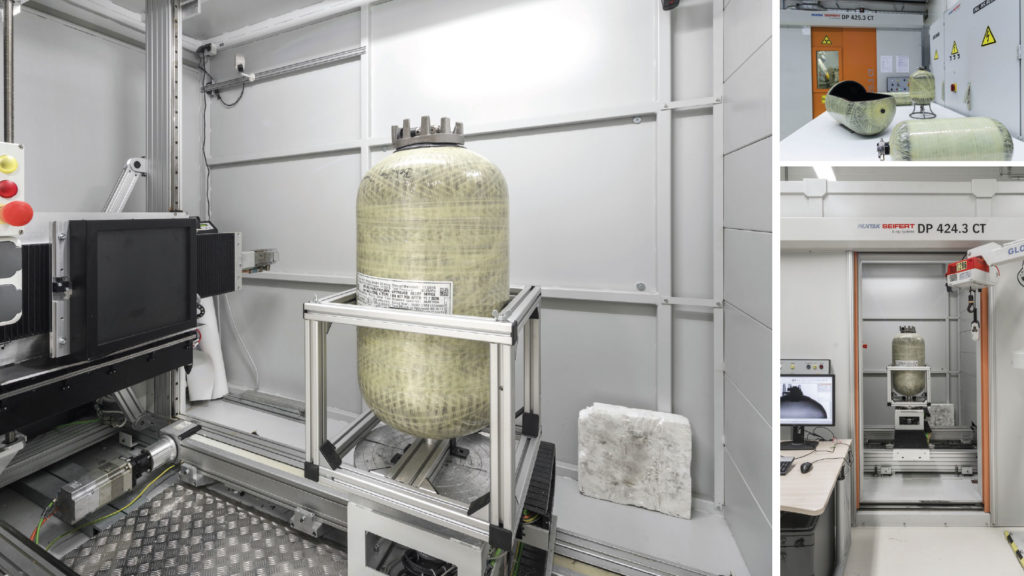
« Le réservoir est composé à l’intérieur d’une chemise synthétique qui assure l’étanchéité. Cela forme une paroi à haute résistance pouvant supporter plus de 200 bars de pression. L’éventuelle faiblesse structurelle va se situer au niveau de la valve vissée à l’extrémité, indispensable pour laisser passer les gaz. En laboratoire, nous procédons depuis 2003 à une batterie de tests sur toutes les pièces, avec des scanners numériques, pour s’assurer de la parfaite adhésion entre chaque élément. On fait tourner nos échantillons à 360° sous des rayons X jusqu’à obtenir 800 images en 3D de chaque élément, sous tous les angles possibles, et ce, sans destruction. Mais nous testons également la résistance de chaque élément en les soumettant aux effets de la pression, d’un froid extrême et de la chaleur, et ce, jusqu’à la rupture, pour voir là encore les faiblesses. On analyse ensuite les déformations par quadrillage pour ne rien laisser passer, et en tirer des conséquences. Certaines de ces techniques de pointe sont issues de l’aéronautique ».
Salle de torture
Voilà donc ce que chaque composant de la future Audi va subir en laboratoire. Puis vient le moment de tout assembler, et de vérifier sur le terrain, lors d’essais longue-durée en grandeur nature, le bien fondé de ces recherches. Un travail de titan, qui commence environ 3 ans avant le lancement de chaque nouveau modèle. Près de 600 préséries ou prototypes sont ainsi discrètement testées, jour et nuit par 2400 essayeurs, auprès de 17 « stations » Audi réparties dans le monde, dans des endroits généralement déserts et reculés par soucis de confidentialité. Les essayeurs vont totaliser plus de 35 millions de kilomètres chaque année, soit près de 700 000 heures d’essais pour faire d’une Audi une Audi ! Werner Zimmermann, notre « monsieur qualité », poursuit…
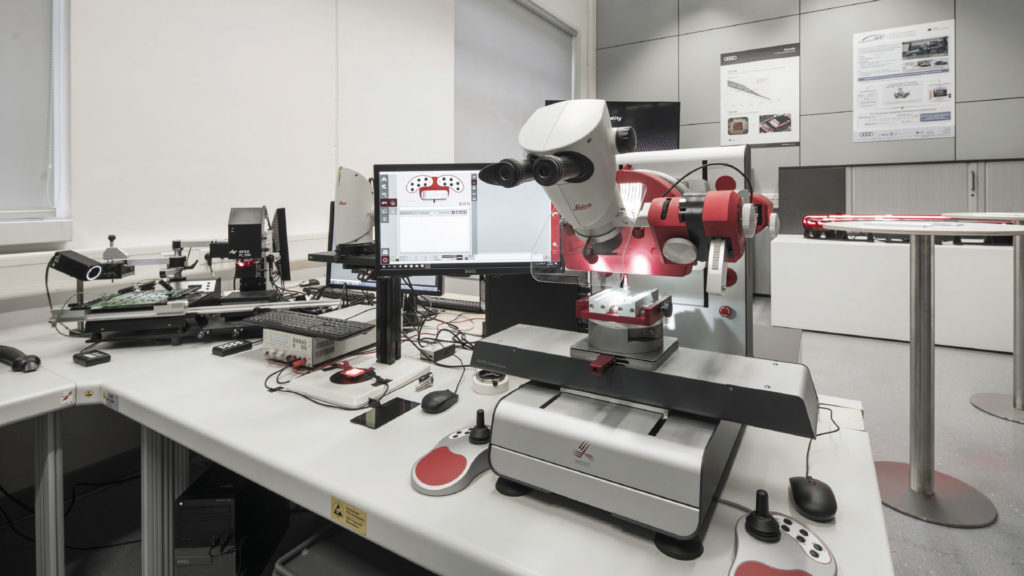
« Chaque voiture est équipée d’un relevé de mesures de la taille d’une petite machine à laver qui pèse environ 35 kg, et qui est arrimé sur la banquette arrière. Cet appareil ne laisse rien passer durant les phases de roulage. Ces collectes sont en très forte hausse avec la multiplication des systèmes électroniques embarqués dans les voitures, notamment les systèmes d’assistance à la conduite. Ainsi, nous obtenions 3 Go de données avec une A3 en 8 jours, mais désormais plus de 50 Go avec une A7 ou A8. Et en 2 minutes, nous enregistrons jusqu’à 60 Go de données avec nos futurs modèles, des mesures qui doivent être ensuite interprétées. Le point critique reste subjectif, avec le ressenti de nos essayeurs, mais nous collaborons aussi étroitement avec des universités et des instituts de psychologie. De nombreuses innovations arrivent dans nos voitures, et avant de valider un nouveau dispositif, nous devons le confronter sur le terrain à toutes les situations possibles ! ».
Ainsi, rien que pour le « park Assist », cet assistant d’aide au stationnement qui aujourd’hui se généralise, nous apprenons qu’il a été ausculté sur 4 canaux bien distincts, avec une mesure de la vitesse d’approche de la voiture, l’état des systèmes d’assistance, la réactivité des divers capteurs et la prise en compte du sens de la marche de l’auto. Plusieurs scénarios sont testés sur le terrain, et une classification des éventuels défauts est faite. L’intégralité des scènes est enregistrée, puis visualisée sous la forme de courbes et graphiques qui sont décortiqués par des experts. Cette année, Audi a déjà collecté 550 terra octets de données. Un « trésor de guerre numérique » soigneusement stocké à Ingolstadt dans de gros serveurs, dont l’emplacement est tenu secret…
Une oreille attentive
Une bonne finition passe bien sûr par la réelle qualité des matériaux et leurs assemblages, mais aussi par une foule de perceptions forcément subjectives, faisant appelle à nos sens. Parmi eux, l’ouïe est constamment sollicitée, et chaque son émis par une Audi est soigneusement étudié. On assiste par ailleurs à une vraie révolution, en passant progressivement du moteur thermique à l’électrique. Avec un bon vieux moteur à explosion, les bruits de transmission, mais aussi de combustion et les vibrations forment un tout, inhérent au thermique. Avec l’électrique, certains bruits masqués auparavant par les basses fréquences deviennent d’un seul coup perceptibles ! Certains sont acceptables, voire agréables, d’autres pas, et la difficulté est de localiser ces bruits, puis d’isoler leur source.
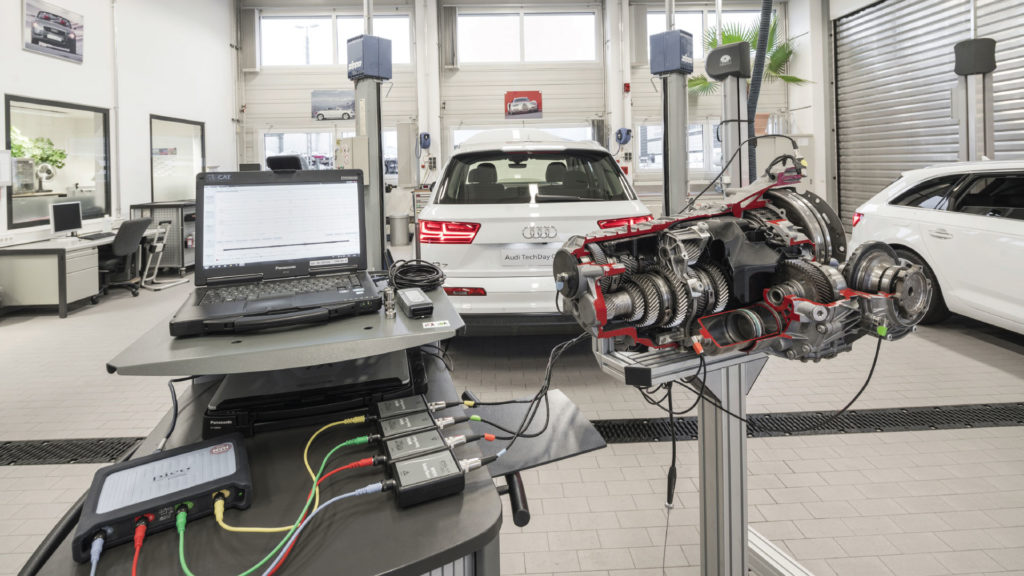
Pour y parvenir, Werner Zimmermann m’entraîne dans un autre bâtiment, dédié à l’acoustique. Ici, d’un claquement de portière à un réglage de molette, rien n’est laissé au hasard ! « On mesure chaque son avec des micros très sensibles, placés à des endroits stratégiques sur un mannequin humain, qui viennent s’ajouter à de nombreux capteurs disséminés dans la voiture, installés à proximité d’endroits générateurs de nuisances sonores, comme les roulements, la boîte de vitesses, l’échappement ou la pompe à carburant. On utilise des accéléromètres pour mesurer les vibrations et les fréquences, pour ensuite les isoler et, si possible, les supprimer. Il en résulte une isolation phonique adaptée à chaque modèle, en fonction de ses spécificités » !
Coup de projecteur
Bien sûr, qui dit « Audi » dit éclairage dernier-cri, ce qui entraîne là encore des contraintes et des batteries de tests que l’on n’imagine pas. Werner Zimmermann apporte ses lumières sur cet aspect… « Audi est un pionnier dans l’utilisation de nouvelles technologies d’éclairage, avec les Matrix LED, les OLED ou les phares laser. Dès le départ, nous travaillons en étroite collaboration avec nos experts qui se rapprochent de nos fournisseurs. Une OLED ne mesure que 2 mm d’épaisseur ce qui ouvre de nouvelles perspective en matière de design et d’éclairage, comme les rétroviseurs extérieurs « virtuels », les écrans de bord avec des animations complexes, etc… Cela nous intéresse, mais on veut bien entendu des éléments de qualité, pouvant résister à toutes les conditions possibles durant au minimum 15 ans (de -40° à + 105°), mais aussi avoir un rendu parfait, ce qui implique une découpe au laser de chaque pièce. La miniaturisation des éléments est un vrai défi et la clé de l’avenir. Nous voulons avoir plus de puissance dans des espaces toujours plus réduits. En ce moment, on essaye de faire des transistors de 10 nanomètres, soit à une échelle dix fois plus petite qu’un… virus ! ».
Avant de lancer un modèle en production, Audi vise la perfection, avec des tolérances minimes. Près de 20 millions de mesures par laser sont réalisées !Voilà qui donne le vertige, mais Audi n’est pas seul à s’aventurer dans cet univers de l’infiniment petit… « Nous sollicitons l’expertise de nos grands fournisseurs, comme NVIDIA, Bosch ou encore INTEL et les poussons à nous suivre. Audi exige des normes de qualité bien supérieures aux normes « grand public ». Ainsi, par exemple, nos dernières voitures utilisent un écartomètre qui scanne la route en permanence, pour détecter les éventuels obstacles. Une diode laser est au cœur de ce système, et là, on travaille sur des couches de l’ordre du micromètre d’épaisseur. Cette pièce, essentielle au bon fonctionnement du dispositif, doit bien sûr résister aux intempéries et vibrations, et il est clair que des particules pourraient altérer ses performances. C’est pourquoi nous procédons pour ce type de pièce à un montage totalement automatisé, qui se fait dans une chambre blanche ».
Rigueur millimétrée
Plus évident pour le grand public, cette belle rigueur est perceptible dans le rendu global de la voiture, avec des ajustages irréprochables entre les panneaux de carrosserie, et des peintures sans défaut. Pour parvenir à cette maîtrise, Audi ne ménage pas, là encore, ses efforts… Werner Zimmermann me fait pénétrer dans une vaste salle réservée à la « métrologie ». Rien à voir avec la RATP, mais plutôt avec la géométrie. « La structure de notre prochaine voiture est posée sur un mètre-gabarit qui sera la référence à retenir pour fabriquer, en série, le modèle sur nos chaînes. C’est une grande plaque en aluminium réglable, et chaque pièce originale est fraisée elle aussi dans le même matériau. Elles sont mesurées à l’aide qu’une quarantaine d’instruments, et notre tolérance est de moins d’un dixième de millimètre, ce qui reste invisible à l’œil nu. On joue également avec les perspectives, que ce soit avec un joint ou un jonc chromé, pour tromper l’œil humain. Ainsi, sur un même joint de portière, entre le haut et la bas, il peut y avoir jusqu’à 4 mm d’écart ! Bien sûr, la numérisation permet de travailler près de 3 ans en amont, pour anticiper et tout bien régler. Mais rien ne vaut le rendu « en vrai », pour tout parfaire et affiner ».
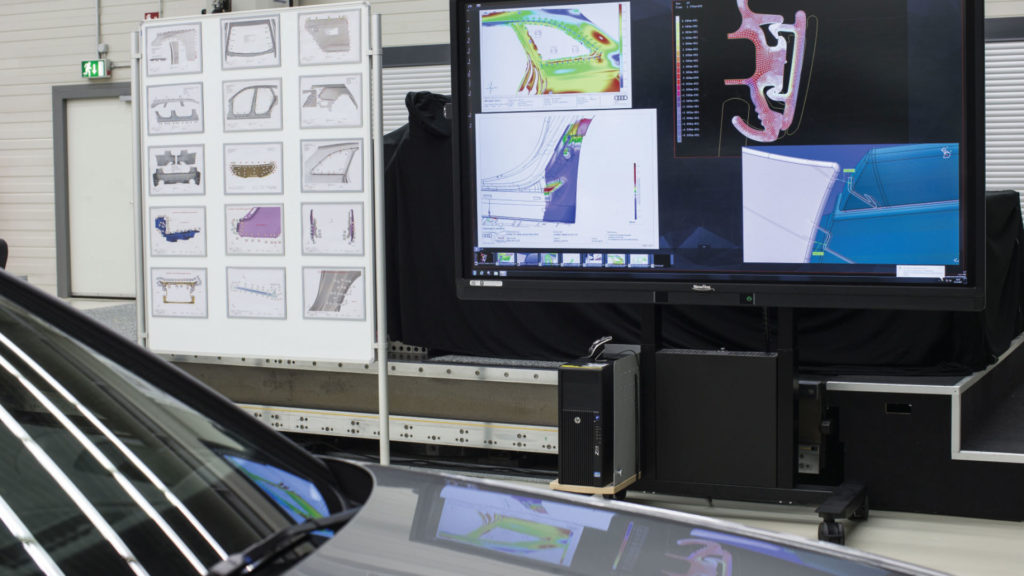
Si l’œil et la main de l’homme restent des outils irremplaçables, les robots apportent dans cette étape une aide précieuse… Face au master de la future A6 que nous découvrons en avant-première, Werner poursuit sa démonstration. « Nous plaçons des capteurs sur toute la voiture, pour ensuite la numériser à l’aide de robots qui travaillent sur 8 axes. On mesure les distances entre chaque élément, mais aussi les surfaces, qui sont scannées. Avant, du temps d’une Audi 80, on avait près de 6000 points de mesure. Désormais, avec cette technologie, rien ne nous échappe puisque nous avons 20 millions de points de mesure, et ce, en une seule prise ! On récolte jusqu’à 100 Go de données pour avoir une image complète et parfaite de la carrosserie, et ce, en à peine 4 heures. S’il y a un écart, ou un défaut, cela apparaît en rouge sur l’écran, l’idéal étant d’avoir du vert partout, signe d’un zéro défaut ».
Une maniaquerie relevant de la « psychiatrie » qui concerne aussi l’intérieur. Et là encore, comme Werner Zimmermann le fait justement remarquer, on assiste à une autre révolution… « Dans l’A4, il y a 22 boutons classiques, tandis que dans la nouvelle A8, il n’en reste plus qu’un ! ». Un nettoyage en règle, qui impose de nouvelles méthodes de travail. « Les écrans ont pris le pouvoir, et il faut maîtriser les joints de ces écrans, qui sont réglés à 5/10e de mm. On traque notamment les fuites de lumière d’ambiance, pour ne pas fausser la perception voulue. Nous procédons à un réglage visuel, tactile et acoustique de tous les éléments constituant le mobilier de la voiture, avec les sources de lumière donc, mais aussi les éventuels bruits aérodynamiques, sans oublier les contours graphiques des éléments. Là encore, la numérisation nous aide, puisque l’on peut modeler et visualiser l’interaction des pièces en mouvement. Cela permet d’évaluer les éventuels défauts très tôt, avant de produire le « master », mais aussi d’atteindre nos objectifs plus vite, tout en respectant nos exigences. Il doit y avoir une harmonie entre les différents matériaux, ce qui implique d’avoir les bons outils pour maîtriser la production et le façonnage de chaque pièce. Une fois que c’est validé, toutes nos données sont ensuite fusionnées, pour élaborer la pièce finale voulue. On peut ensuite envoyer ces données à nos fournisseurs ou 1800 partenaires partout dans le monde, en quelques clics. Reste ensuite le plus grand défi : mettre en place ces technologies sur les chaînes d’assemblage. C’est un vrai challenge, dans la mesure où rien qu’à Ingolstadt, on produit une voiture toutes les 80 secondes par ligne pour le monde entier, et qu’il y a trois chaînes d’assemblage ! »
Une rigueur « 2.0 »
Il paraît difficile, vu le niveau de rigueur atteint, d’aller encore plus loin. Pourtant, Audi planche dès aujourd’hui sur la voiture et les services du futur. Et selon Werner Zimmermann, le futur, c’est déjà demain ! « Les voitures sont de plus en plus complexes, en embarquant de nouvelles fonctionnalités, et elles vont communiquer en temps réel avec des infrastructures connectées. On vise désormais un service technique « 4.0 », à l’aide une fois de plus de la numérisation. On veut que les logiciels embarqués dans nos voitures se mettent quotidiennement à jour, de façon autonome. Dès 2018, la prochaine Audi e-tron quattro disposera d’un analyseur, une véritable « boîte noire » qui va collecter de nombreuses données. Elles vont permettre d’offrir un entretien sur-mesure à chaque client, en fonction de sa typologie et de l’usage qu’il fait de sa voiture, tout en faisant des projections sur les prochaines pièces à remplacer ». Avec de telles techniques de pointe, qui ne laissent rien au hasard, Audi devrait sans aucun doute conforter sa place dans le monde impitoyable du « premium », et toujours faire autorité dans le domaine de la finition. Car c’est en pratiquant quotidiennement cette « haute résolution » que le constructeur aux Anneaux fera en sorte que ses clients fassent preuve d’une « haute fidélité »…
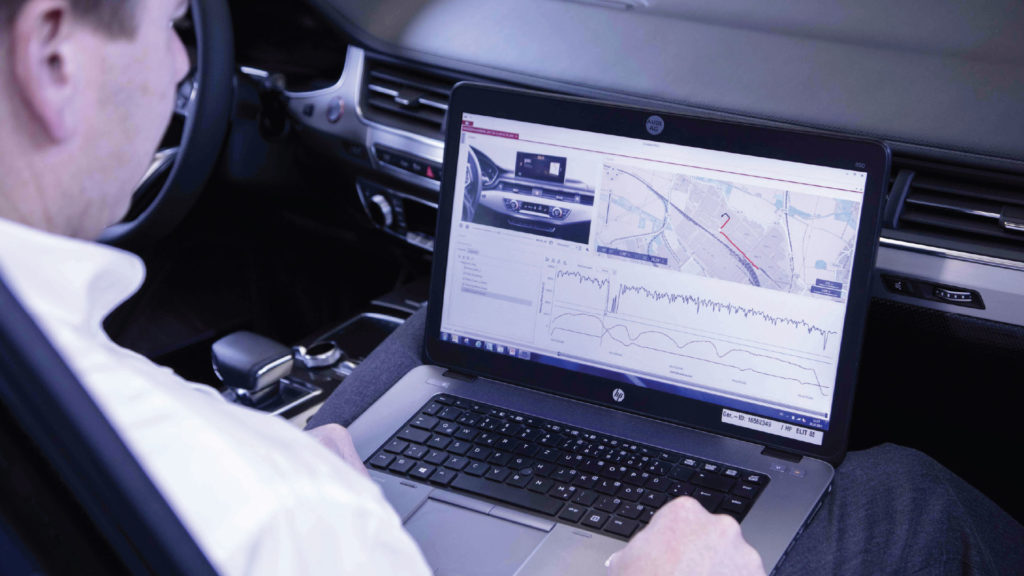